Gate Valves
The gate valve is considered to be the most popular style of valve in the world of flow control. It is a type of valve having a gate that moves perpendicular to flow of the service and hence the name. A gate valve is usually used as a shut-off valve. In the up position, the valve is open. In the down position, the valve is closed.
It is also known by other names like knife valve or slide valve or stop or block valve as its primary purpose is to stop the flow. This valve has become an important piece of fluid control equipment for more than 150 years. In fact, this was the first valve patent issued in the United States. The gate valve has become a one-stop solution for fluid control call with relatively little basic design change
Materials used:
- Gun Metal
- Cast Steel
- Stainless Steel
- Cast Iron
- Alloy Steel
- Brass
- Bronze
- Aluminum
- Zirconium etc.
Buying tips:
- Material
- End connection
- End usage
- Sizes
- Pressure grade
- Standard
- Corrosion or abrasion resistant
- Durability
|
Types of gate valves:
There are two types of gate valves depending on the disc design. They
are:
- Parallel gate valve: This uses a flat disc gate between
two parallel seat—up upstream and downstream. Parallel gate
valve is widely used the pipeline industry. Unlike the wedge gate
valve, the parallel gate valve needs some assistance to seal
properly which is usually done in the form of a spring loaded or
mechanically activated spreading action between the two disc halves.
These types of valve design can fit into angularly or asymmetric
misaligned valve seats.
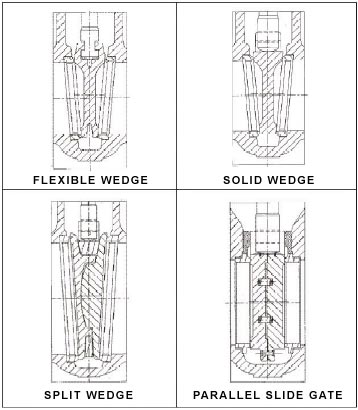
A diagrammatic representation of different types of pipe valves.
- Wedge-shaped gate valve:
This type of valve is of three types:
- Solid wedge: The solid wedge is the oldest
form of gate valve and a drawback to this design is that it does
not have any flexibility. There is the chance of solid disc
getting jammed in the seats if there is any valve body/seat
distortion due to extreme temperature fluctuations.
- Flexible wedge: With the addition of a
groove or slot around its periphery, the flexible wedge gate
valve can adapt to temperature changes and adverse piping
stresses without binding. This design is little easier to
manufacture and is the most common type seen on commodity gate
valves used in industrial applications.
- Split wedge: This is of a two-piece design
having mating surfaces on the back side of each disc half. This
allow the downward stem thrust to be uniformly transferred to
the disc faces and onto the seats. This provides protection
against jamming due to thermal expansion.
Designs of gate valves:
There are five popular body/bonnet joint designs in gate valves. They
are:
- Screwed: This is the most simple design available and it
is used for inexpensive valves.
- Union: This design allows for easier disassembly for
repair and maintenance.
- Bolted-bonnet: The most popular design and used in large
number of gate valves. This requires a gasket to seal the joint
between the body and bonnet.
- Welded-bonnet: This is a popular design where disassembly
is not required. They are lighter in weight than their bolted-bonnet
counterparts.
- Pressure-seal: The higher the body cavity pressure, the
greater the force on the gasket in a pressure -seal valve. They are
used extensively for high-pressure high-temperature applications.
Uses of gate valves:
Gate valves are useful in applications involving slurries. This is
because their “gates” can move right through the slurry. Other
than that, they are used in applications that involve viscous liquids
like:
- heavy oils
- varnish
- light grease
- steam
- oil
- gas
- natural gas
- honey
- molasses
- cream non-flammable viscous liquids
- high pressure, high temperature steam applications
Repair & Maintenance of Gate Valves:Certain care
should be taken for proper functioning of gate valves such as
follows:
- Since gate valves are used in harsh environments, these
valves need to be repaired. This decision as to whether to
repair or replace a gate valve usually depends on comparing the
replacement cost to the repair cost. When the repair cost is
more than than 50-65% of the cost of a new valve, it is better
to replace the valve, unless the delivery is unacceptable.
- For better performance, it is a good practice to use the gate
valve three or four times a year.
|
Industrial applications:
Gate valves play an important role in virtually every:
- chemical plant
- refinery
- pipeline industry
- salt working pipelines
- power industry and any other
- industrial facility in the world
The points mentioned below will be a guide for the buyers: